クルマの性能を
左右する電池。
そのものづくりに
賭ける思い。
トークメンバー
- Y.H. 製造
1999年関連会社に入社し2014年より現職に転籍。リチウムイオン電池の正極板と負極板を製造する源泉工程の職長として、主に工程全体の管理やマネジメントに携わる。トラブル対応の際は、品質管理、製造技術、保全部門など他部署とも連携しながら改善活動を推進。
- K.H 開発・設計
2015年新卒入社。新規VEセル開発リーダーとして、負極材料の開発、源泉工程および活性化工程などの対応に携わる。先行開発部門で開発された要素的な材料の製品化にあたっては、メーカーと協業して電池のスペックを決定する役割を担う。
- T.M. 生産技術
2017年キャリア入社。電池の設計仕様書に基づき、製造装置の構想と開発を担当。現在の部門に所属する以前は、新規工場立ち上げプロジェクトの一員として、電池の設計指示書に従い量産ラインの設計・導入立ち上げをメーカーと検討する役割を担った。
- H.S. 品質管理
2019年キャリア入社。2022年より主に活性化工程以降の後工程における不具合の未然防止及び再発防止に注力。現在は新居第3工場の生産準備グループで品質管理に携わる。工場の立ち上げ時や量産開始の前後など、状況に応じて様々な部署と連携しながら品質管理に取り組む。
- H.K. 先行開発
2023年キャリア入社。前職は電子部品メーカーに勤務。トヨタバッテリーではシミュレーションを活用した材料や電池の解析業務を担当。シミュレーションで得られた知見から、電池の性能アップに向けたより高性能な材料の開発・提案をすることがミッション。
トヨタバッテリーの
技術職の醍醐味とは?

今日集まったメンバーは蓄電池の分野に従事しているという共通点はありますが、仕事内容はまったく異なります。まずは皆さんのお仕事の面白さや大変さ、やりがいをお聞きしたいです。
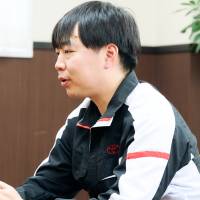
品質管理の仕事の一番のやりがいは、一つでも多く不良品を減らし、良品を増やすことに尽きますね。
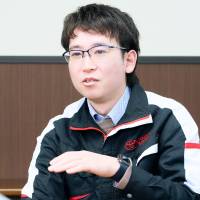
不良品を減らすために、通常の業務以外でどういった取り組みをすることがありますか?
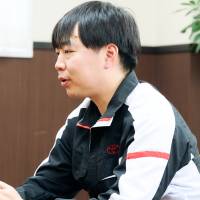
以前、活性化工程などの後工程を担当した際には、車両工場への影響を少しでも軽減できるよう、製品の迅速な良否判断に努めました。当初は不良懸念品と判定された製品を、詳細なデータに基づき良品として再認定して出荷できた際には、他部署から非常に多くの感謝の言葉をいただきました。
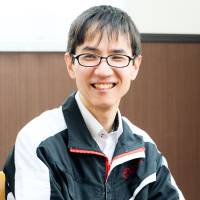
トヨタバッテリーは厳格な基準で製造に取り組んでいるので、良品の基準を相当厳しく設定していますからね。
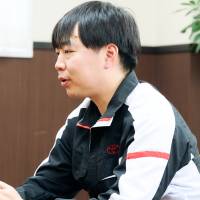
はい。当初はそうした基準から外れた製品の中には、顧客との取り決めや規格を加味して、良品として再認定できるものがあるんです。
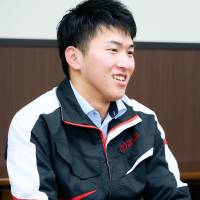
なるほど。開発・設計のKさんは、どんなところにやりがいを感じていますか?
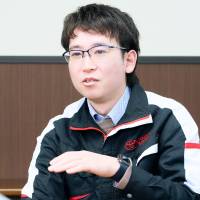
定められた開発期間内で電池を設計するには、生産技術からの仕様要求と、顧客とのスペック合意との間で、着地点を見出す必要があります。そうした大変な期間を乗り越えて、世に電池を送り出した瞬間に、大きなやりがいを感じます。Tさんはどうですか?
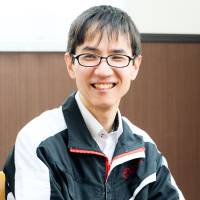
私製造装置のコントロールに面白さを感じています。例えば、1万個の製品の中に1個だけ不良品が発生した際の原因究明は、装置のわずかなブレを突き止めなければなりません。温度変化や振動など、もはや自然現象との戦いです。こうした不安定な状態をいかに安定させるかが、装置を設計する生産技術の腕の見せどころになります。

Hさんはいかがですか?先行開発は開発内容に研究的な要素が加わる場合もあるので、他部署とは毛色の違ったやりがいがありそうですが。
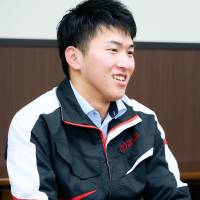
そうですね。担当業務のひとつに、開発過程での困りごとをシミュレーションで解決するというものがあります。電池の中の現象は本来目視することはできませんが、シミュレーションを活用すれば、材料内で原子が並んでいる様子やイオンの動きが可視化できます。このような技術を使って電池内部の現象を解き明かすところが面白いですね。
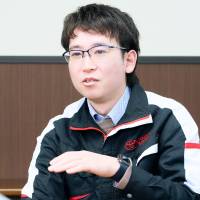
私は先行開発の方が開発した要素材料の製品化にも携わっていますが、先行開発はそういったシミュレーションも行うんですね。こうしたシミュレーションや設計、開発などを経て、Yさんの製造部門にバトンが渡っていくわけですが、製造のやりがいはどんなところにありますか?

やはり、顧客に製品が渡って、それを使ってもらえることが一番ですね。あと、これは大変な部分でもあるのですが、製造は「安全に、より品質のいいものを、より効率良く」を追求する部門です。そのために改善を続けてロスを減らしていくのですが、うまく減らせれば数字に明確に表れるので、そうした点にも面白さを感じますね。
部署間の連携と、
品質に対する思い。
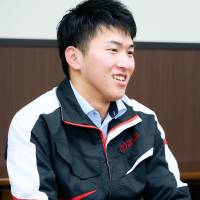
製造のYさんがよく連携するのは、どういった部門ですか?

改善に取り組む際には、必ずと言っていいほど品質管理の方と連携しますね。
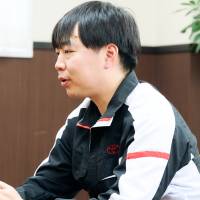
そうですね。あと、先ほど良品に再認定する際のお話をしましたが、その対応には製造の方の協力が欠かせません。

不良ロスが減らせるような対応は、現場としても大きなやりがいの一つなんです。品質管理の方にチェックポイントを尋ねるのはもちろん、設備の設定や制御方法を製造技術の方と検討したり、材料に関する問題を技術部門の方に相談したりするなど、様々な部署と協力して取り組んでいます。
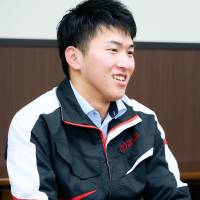
なるほど。生産技術のTさんも、設備を扱う仕事なだけに現場をはじめ、いろんな部門と関わることが多そうですね。
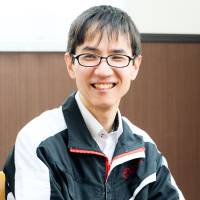
はい、設備トラブルに関する問い合わせは日常的にありますから。ただ、問い合わせの中には胸が痛くなるものもあって・・・。
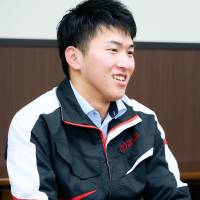
なんだか不穏ですね(笑)。それはどんな問い合わせですか?
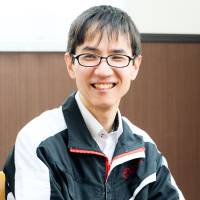
以前、原因不明のエラーで装置の部品が壊れ、生産がストップしたことがあったんです。一分一秒を争うような状況で答えが見えなくて、本当に焦りました。
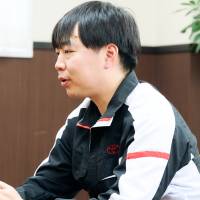
その気持ち、わかりすぎて私も胸が痛いです(笑)。今のお話のように、設備不良の場合は生産技術に連絡が行くんですが、品質不良の場合は品質管理に直接連絡が来ます。特に顧客から問い合わせが来るのが、品質管理として納入不具合は一番避けるべき事態ですので、ドキリとしますね。いかにスピーディーな解決ができるかが我々の手にかかっていますし、各部門との連携が欠かせません。
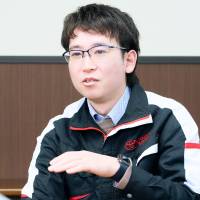
ちなみに顧客から連絡が来るケースって、どれくらいの頻度でありますか?
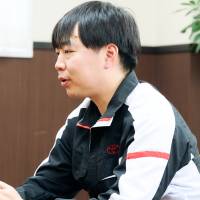
単なる問い合わせといった場合もあるので一概には言えませんが、年に数件といったところでしょうか。

当社では年間に車両数百万台分もの蓄電池を製造しますよね。そのうちの1桁ということは、わずかな異変も見逃さない懸命な努力が必要になりますね。
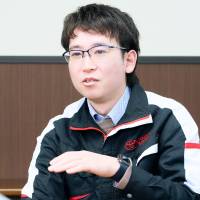
でも確かに、安全と品質が最優先という考えが全社に根付いていますよね。
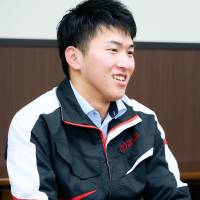
実際に安全第一、品質第一という言葉が常に飛び交っていますしね。
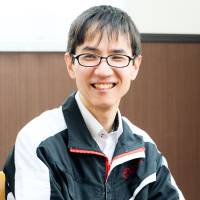
私たちの電池はクルマに搭載されるものなので、いわばエンドユーザーの命に関わります。それを考えると、絶対に妥協できませんからね。
トヨタバッテリーの魅力と、
活躍できる人物像。
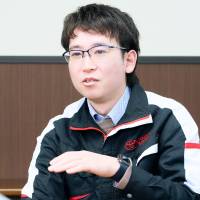
自動車は年々進化して燃費も向上しています。私たちの使命は、その燃費を良くするために電池の性能を上げ続けることです。新しい電池を世に出してクルマの性能が上がることで、世のお客様に喜びを還元できることに、この会社で働く魅力を感じています。

完成車メーカーと連携しているので、自分のものづくりが世界に広がっていく実感がありますよね。あと、これから先も拠点がどんどん増えていくと思うので、会社の成長も魅力の一つだと思います。毎年工場が増えていますし、Hさんも新居第3工場の立ち上げをされていますよね。
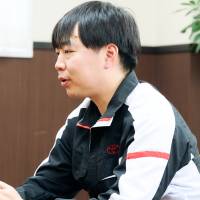
そうですね。こうした成長や変化の激しさも含めて面白い会社だと感じています。
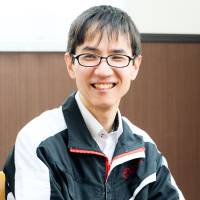
毎年のように生産ラインを導入できる業界や会社って、そう多くはありません。それができる会社でものづくりをしていると、自分の業務に上向き志向で取り組めていると実感します。
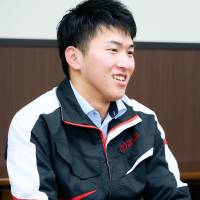
私は前職で、超小型の電子部品を開発していたので、エンドユーザーに届くまでのプロセスがイメージしづらいところがありました。ですが今、開発している電池はトヨタ自動車をはじめとしたクルマに搭載され、世の中の至る所でそのクルマが走っています。開発に携わった製品が、世の中に浸透しているのを明確にイメージできることも、魅力だと思います。

ちなみに、トヨタバッテリーで活躍できるのは、どういう方だと思いますか?
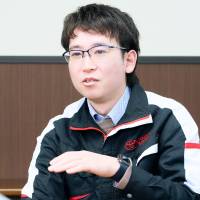
開発・設計は、いろんな部署や社外の方と会話をすることが多いので、物怖じせず会話ができる方がいいですね。その方が、いろんな人々と話す過程で多くの知識を吸収できるので、成長も早いと思います。
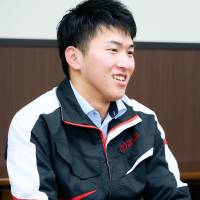
先行開発は新しい技術に関わる部署なので、好奇心のある方が向いていると思います。いろんなことに興味を持って、他部署の方の仕事にも視野を広げることで、思いもよらなかった新しい発想や連携が生まれるからです。
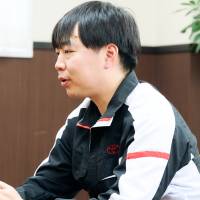
品質管理の仕事は「トラブル発生」というマイナスからスタートすることが多く、だからこそ、過剰にストイックになるとつらく感じるかもしれません。もちろん責任感を持って進めることは重要ですが、社内にはいろんな部署があって、状況に応じて手を貸してもらえるので「何とかなる」くらいの心持ちでどっしりと構えていられる方が向いていると思います。
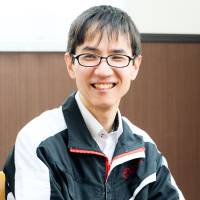
生産技術は、学ぶ意欲の強い方に向いていますね。この職種は、社会人になってからの方が学ぶことが多いので、あらゆる分野の知識に対して幅広くアンテナを張って、常に学び続けられる方が向いていると思います。

みなさんありがとうございます。製造部門の立場からだと、私が思うのは前向きに動いてくれる方がいいですね。どこの部署でもそうだと思いますが、自分自身が成長できるように、資格取得や改善など、いろんなことに前向きに取り組んでほしいです。
同じ目的に向かう
仲間として、
お互いにかけたい言葉。
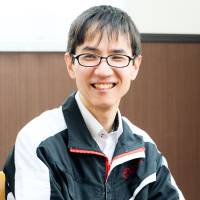
せっかくこうして集まったので、最後にお互いに何か言いたいことはありますか?

品質管理の皆さん、しょっちゅう呼び出してごめんなさい!
(笑)
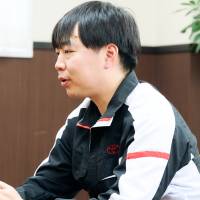
いえいえ、むしろトラブル対応をする中で学べることや繋がる縁がありますので、どんどん頼ってもらいたいです!
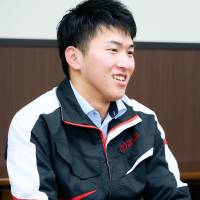
自分の担当業務がシミュレーションであるため直接電池を触る機会が少ないので、皆さんには「日々製品を作っていただき、ありがとうございます」という感謝を伝えたいです。電池を製品化し、生産してくださる方々がいるからこそ、自分たちの要素技術が、世に出た製品の中で生きるわけなので。
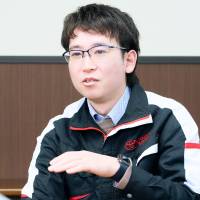
自分は感謝という意味で言うと、製造の方に対する思いが大きいですね。新しい電池を開発する際、量産の設備で実験をするので、生産を止めていただく必要があります。そういうときにも嫌な顔をしないどころか、相談にも乗ってくださるので、本当に感謝しています。

お気軽にお越しください(笑)。どんどん相談していただければと思っていますし、協力も惜しみません。
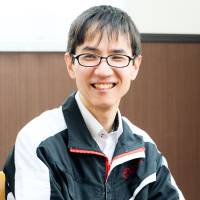
世の中を豊かにできる電池を作っていくために、これからも部署の垣根を越えて協力していきたいですね。