電池ができるまで
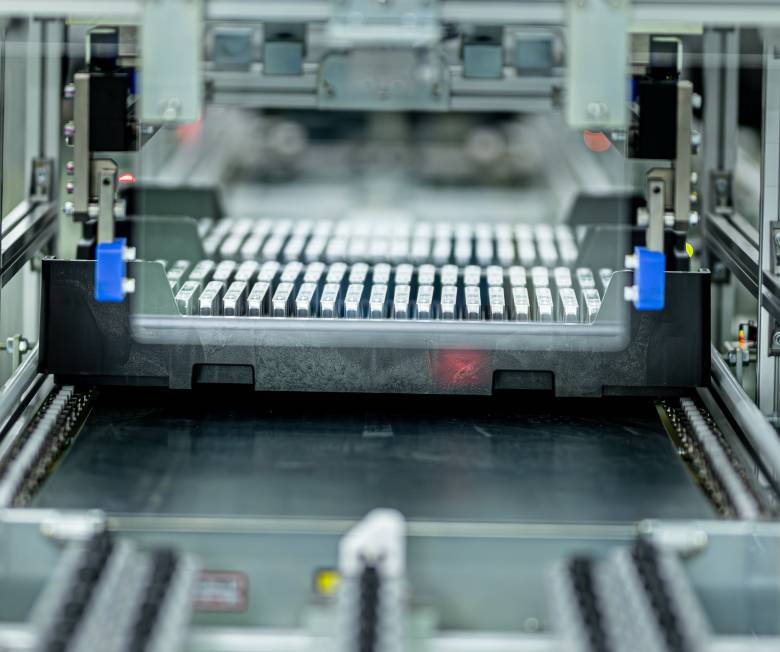
電池の製造工程
バッテリーは大きく分けて「電極」「組付け」「活性化」「パック」の4つの工程で作られています。各工程を経て、「高い品質と性能を併せ持つ安全なバッテリー」をお客様のもとに出荷するまでの流れをご紹介します。
-
Flow 01
電極
バッテリーの電極となる正極板と負極板を作る工程です。粉末材料を混練機に入れ、液体と共に混ぜ合わせ、ペーストを作製します。次に金属箔の表面にペーストを薄く均一に塗り、乾燥炉で乾かします。その後、ロールプレスで圧力をかけて目標の厚みまで圧縮し、目標の幅にスリットして完成です。
-
Flow 02
組付け
各種部品を組み付けて、電池セルを作製する工程です。正極板、負極板、セパレータを重ね合わせて捲回し電極体を作製します。電極体に端子を接合し、ケースに納めて溶接します。それを乾燥炉で乾かした後に、電解液を注入・封止してセルが完成します。
-
Flow 03
活性化
セルを充電・放電し、電池セルとして完成させる工程です。繰り返し充電・放電することでセルを安定化させます。その後、不良品を流出させないように、一つひとつすべての製品を検査する全数検査を行います。
-
Flow 04
パック
車載用のバッテリーパックを作製する工程です。複数のセルを接続し、各種部品を組み付けてバッテリーパックを作り上げていきます。出来上がったバッテリーパックは、出荷前の全数検査を経て、お客様である自動車メーカーの元に運ばれます。
高品質・大量生産を両立する
モノづくり
一つの電池は複数のセルで構成されているため、生産ラインには極めて高い生産能力が求められます。そのため当社では、より良い製品をより多く生産するためのさまざまな施策に継続して取り組んでいます。ここでは高品質・大量生産を実現する私たちのモノづくりのポイントについてご紹介します。
-
工程の小型化による生産性の向上
かつて当社の生産工場や各工程は重厚・長大で、一つの工程に非常に大きなスペースを要していました。この課題の解決のために、各工程の省スペース化を図りながら生産性を向上させる取り組みを開始。各工程の生産能力の飛躍的な向上を実現しました。電極工程を例に挙げると、従来の工程の半分以下にまで小型化しながらも、生産能力を倍にすることに成功しています。
-
設備の自動化による業務量削減
設備は基本的にすべて自動化しており、工程によっては一人の作業者で生産が賄えるほど省人化が進んでいます。作業者の主な仕事は材料のセットや完成品の取り出し、品質確認のための抜き取り検査などに限られるため、電池製造の工程におけるヒューマンエラーの発生抑止と生産性の向上につながっています。
-
異物混入を許さない
レーザー溶接技術と生産環境一般的にアルミ材料へのレーザー溶接は困難で、溶接漏れによる異物混入が発生しやすいとされています。当社は長年にわたる研究により、「レーザー学会産業賞」の貢献賞を受賞するほどの高度なレーザー溶接技術を確立し、溶接漏れを大幅に削減。
また、製造現場ではグリーン・イエロー・レッドの色によって厳格なエリア分けを行うなど管理を徹底。技術面・管理面の両面からのアプローチで、異物混入の徹底排除に成功しています。